在实行cnc加工程序前主要先进行对刀以肯定起始点位置,而对刀通常是操纵者颇感头痛的事情,刀具刃磨后又要从头对刀,刀具的刀尖磨损,独特是多把刀进行加工时,还需测刀补值。
1.点动对刀发
cnc加工设备按管制面板上的点动键,将刀尖轻触被加工件表面(X和Z两个目标分两次进行点动),计数器清零,再退到需设定的初始位置(X、Z设计初值),再清零,得到该刀初始位置。依序肯定每把刀的初始位置,经试加工后再调节到准确的设计位置(起始点)。这种方式无须任何辅具,唾手就可操纵,但时光较长,独特是每修磨一次刀具就一定从头调节一次。
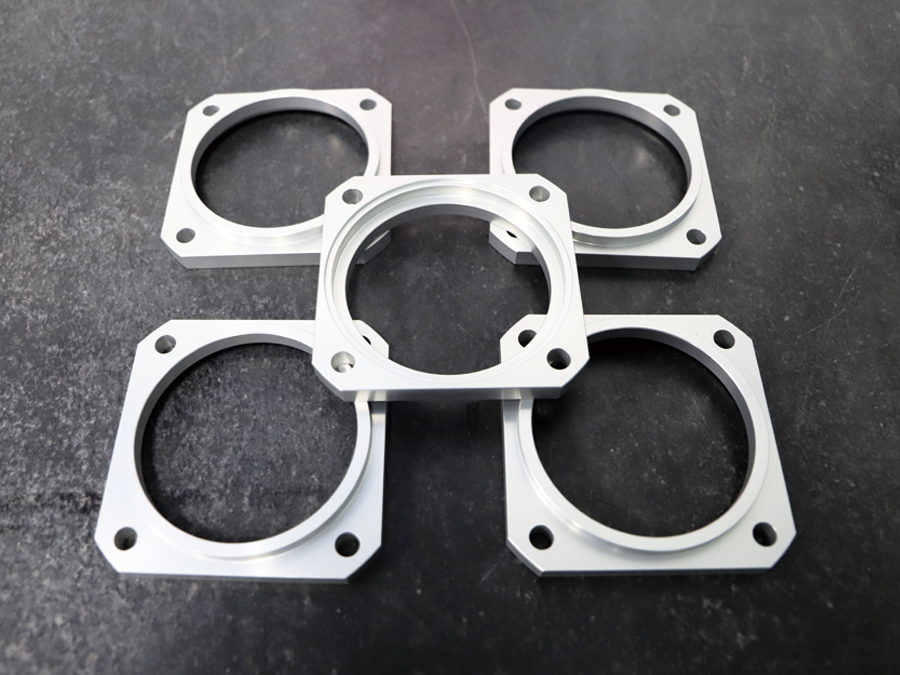
2.选用对刀仪
现在很多车床上都装备了对刀仪,运用对刀仪对刀可罢免丈量是发生的偏差,大大升高了对刀精度,由于运用对刀仪不妨自动计算各把刀的刀长和刀宽的差值,并将其存入体系中,在加工此外的零件的时辰就只需求准则刀,如此就大大节俭了时光。需求关注的是运用对刀仪对刀通常都没有准则刀具,在对刀的时辰先对准则刀。其缺点是选用对刀仪需求添置对刀仪辅助设备,本钱较高,装卸费力。
3.选用数控刀具
cnc加工刀具安装初次定位后,在进过一段时光切削后发生磨损而需求刃磨,寻常刀具刃磨后从头安装的刀尖位置发生了转变,需求从头对刀,而数控刀具的特点是刀具制造精度高刀片转位后反复定位精度在0.02mm控制,大大减少了对刀时光,同时,刀片上涂有金属层(Sic、Tic等)使其耐用度大大升高,可是这个本钱也有点高。
4.用对刀块对刀,选用自控对刀法
用塑料、有机玻璃等制成的简单对刀块课简便的完成刀具刃磨后的反复定位,可是定位精度较差平常在0.2~0.5mm,单任不失为一种迅速的定位方式,再用调节就可以很快很简便。